【www.myl5520.com--爱国名言】
第六章 数控机床常见机械故障及其维修
篇一:数控机床皮带松动
第7章 数控机床常见机械故障及其维修
数控机床机械部分的故障与普通机床机械部分的故障有许多共同点,因此在对机械故障进行诊断及维修时,有许多地方是相通的。但是,数控机床大量采用电气控制与电气驱动,这就使得数控机床的机械结构与普通机床的机械结构相比有很大的简化,使其机械结构的故障呈现出一些新的特征。在实际中,机械故障的种类繁多,本章只能介绍一些共性的部件故障,如主传动系统、进给系统、机床导轨等。
本章首先介绍数控机床主传动系统与主轴部件的故障诊断与维修;然后介绍进给系统的二个主要部件——滚珠丝杠副和导轨副的故障诊断与维修。由于滚珠丝杠副和导轨副时为适应数控机床的特殊要求而特有的,因此对它们的结构及材料性能作了一些介绍,以便读者了解;最后介绍刀库及换刀装置的故障及维修。
7.1数控机床主传动系统与主轴部件的故障诊断与维修
数控机床的主传动承受主切削力,它的功率大小与回转速度直接影响着机床的加工效率。而主轴部件是保证机床加工精度和自动化程度的主要部件,它们对数控机床的性能有着决定性的影响。
由于数控机床的主轴驱动广泛采用交、直流主轴电动机,这就使得主传动的功率和调速范围较普通机床大为增加。同时为了进一步满足对主传动调速和转矩输出的要求,在数控机床上常采用机电结合的方法,即同时采用电动机调速和机械齿轮变速这两种方法。
7.1.1主传动系统
数控机床的主传动系统常采用的配置形式有:
1、带有变速齿轮的主传动
滑移齿轮的换挡常采用液压拨叉或直接由液压缸带动,还可通过电磁离合器直接实现换挡。这种配置方式在大、中型数控机床中采用较多。
2、电动机与主轴直联的主传动
其特点是结构紧凑,但主轴转速的变化及转矩的输出和电动机的输出特性一致,因而使用受到一定的限制。
3、采用带传动的形式
这种形式可避免齿轮传动引起的振动和噪声,但只能用在低扭矩的情况下。这种配置在小机床中经常使用。
4、电主轴
电主轴通常作为现代机电一体化的功能部件,采用在高速数控机床上,其主轴部件结构紧凑,重量轻,惯量小,可提高起动、停止的响应特性,有利于控制振动和噪声,缺点是制造和维护困难且成本较高。
7.1.2主轴部件
数控机床主轴部件是影响机床加工精度的主要部件,要求主轴部件具有与本机床工作性能相适应的高回转精度、刚度、抗振性、耐磨性、和低的温升,其结构必须很好的解决刀具和工具的装夹、轴承的配置、轴承间隙调整和润滑密封等问题。
数控机床的主轴部件主要有以下几个部分:
主轴本体及密封装置、支承主轴的轴承、配置在主轴内部的刀具卡进及吹屑装置、主轴的准停装置等。
主轴的结构根据数控机床的规格、精度采用不同的主轴轴承。一般中小规格的数控机床的主轴部件多采用成组的高精度滚动轴承;重型数控机床采用液体静压轴承;高精度数控机床采用气体静压轴承;转速达20000r/min的主轴采用磁力轴承或氮化硅材料的陶瓷滚珠轴承。
1、主轴润滑 为了保证主轴有良好的润滑,减少摩擦发热,同时又能把主轴组件的热量带
走,通常采用循环式润滑系统。用液压泵供油强力润滑,在油箱中使用油温控制器控制油液温度。现在许多数控机床的主轴采用高级锂基润滑脂封闭方式润滑,每加一次油脂可以使用7~10年,简化了结构,降低了成本且维护保养简单,但是需要防止润滑油和油脂混合,通常采用迷宫式密封方式。为了适应主轴转速向更高速化发展的需要,新的润滑冷却方式相继开发出来。这些新的润滑冷却方式不单要减少轴承温升,还要减少轴承内外圈的温差,以保证主轴热变形小。
①油气润滑方式。 这种润滑方式近似于油雾润滑方式,所不同的是,油气润滑是定时定量的把油雾送进轴承空隙中,这样既实现了油雾润滑,又不至于油雾太多而污染周围空气;后者则是连续供给油雾。
②喷注润滑方式。 它用较大流量的恒温油(每个轴承3~4L/min)喷注到主轴轴承,以达到润滑冷却的目的。需要特别指出的是,较大流量的油,不是自然回流,而是用排油泵强制排油,同时,采用专用高精度大容量恒温油箱,油温变动控制在±0.5℃。
2、防泄漏
图7-1所示为卧式
法兰盘4和5上开沟槽及泄漏孔,当喷入轴承2被法兰盘4内壁挡住,并经过其下部的泄油孔9和套筒3油斜孔7流回油箱,少量油液沿着主轴6离心力的作用下被甩至法兰盘4的沟槽内,经过回油斜孔7流回油箱,达到了润滑介质防泄漏的目的 当外部切削液、切屑及灰尘等沿主轴6与法兰盘5隙进入时,经法兰盘5的沟槽由泄漏孔7排出,少量的切削液、切屑及灰尘进入前锯齿沟槽,在主轴6高速旋转的离心力作用下仍被甩至法兰盘5的沟槽内由泄油孔7排出,达到了主轴端部密封的目的。
要使间隙密封结构能在一定的压力和温度范围内具有良好的密封防泄漏性能,必须保证法兰盘4和5与主轴及轴承端面的配合间隙符合如下条件。
①法兰盘4与主轴6的配合间隙应控制在0.1~0.2mm(单边)范围内。如果间隙偏大,则泄漏量将按照间隙的3次方扩大;若间隙过小,由于加工及安装的误差,容易与主轴局部接触使主轴局部升温并产生噪声。+
②法兰盘4内端与轴承端面的间隙应控制在0.15~0.3mm之间。小间隙可使压力油直接被挡住并沿法兰盘4内端面下部的泄油孔9经回油斜孔7流回油箱。
③法兰盘5与主轴的配合间隙应控制在0.15~0.25mm(单边)范围内。间隙太大,进入主轴6内的切削液及杂物会显著增多,间隙太小,则容易与主轴接触。法兰盘5沟槽深度应大于10mm(单边),泄漏孔7应大于Φ6mm,并位于主轴下端靠近沟槽内壁处。
④法兰盘4的沟槽深度应大于12mm(单边),主轴上的锯齿尖而深;一般在5~7mm范围内,以确保具有足够的甩油空间。法兰盘4处的主轴锯齿向后倾斜,法兰盘5处的主轴锯齿向前倾斜,
⑤法兰盘4上的沟槽与主轴6上的护油槽对齐,以保证被主轴甩至法兰盘沟槽内腔的油液能可靠地流回油箱。
⑥套筒前端的回油斜孔7及法兰盘4的泄油孔9流量为进油孔1的2~3倍,以保证压
力油能顺利地流回油箱。
(3)刀具夹紧 在自动换刀机床的刀具自动夹紧装置中,刀具自动夹紧装置的刀杆常采用7:24的大锥度锥柄,既利于定心,也为松刀带来方便。用蝶形弹簧通过拉杆及夹头拉住刀柄的尾部,使刀具锥柄和主轴锥孔紧密配合,夹紧力达10000N以上。松刀时,通过液压缸活塞推动拉杆来压缩蝶形弹簧,使夹头张开,夹头与刀柄上的拉钉脱离,刀具就可拔出进行新、旧刀具的更换,新刀装入后,液压缸活塞后移,新刀具又被蝶形弹簧拉紧。在活塞推动拉杆松开刀柄的过程中,压缩空气由喷气头经过活塞中心孔和拉杆中的孔吹出,将锥孔清理干净,防止主轴锥孔中掉入切屑和灰尘,把主轴锥孔表面和刀杆的锥柄划伤,同时保证刀具的正确位置。
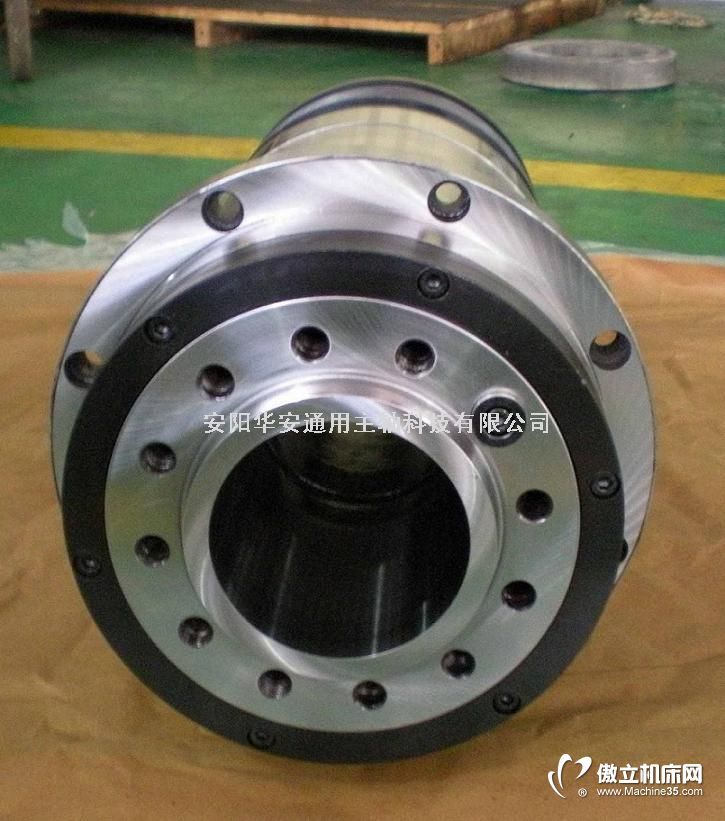
7.1.3主传动系统的常见故障及排除方法(见表7-1)
表7-1 主传动系统的常见故障及排除方法
例1. 主轴噪声的故障维修
故障现象:车床CK6140在1200转时,主轴噪声变大
分析及处理过程:CK6140采用的是齿轮变速传动。一般来讲主轴产生噪声的噪声源主要有:齿轮在啮合时的冲击和摩擦产生的噪声;主轴润滑油箱的油不到位产生的噪声;主轴轴承的不良引起的噪声。将主轴箱上盖的固定螺钉松开,卸下上盖,发现油箱的油在正常水平。检查该挡位的齿轮及变速用的拨叉,看看齿轮有没有毛刺及啮合硬点,结果正常,拨叉上的铜块没有摩擦痕迹,且移动灵活。在排除以上故障后,卸下皮带轮及卡盘,松开前后锁紧螺母,卸下主轴,检查主轴轴承,检查中发现轴承的外环滚道表面上有一个细小的凹坑碰伤,更换轴承,重新安装好后,用声级计检测,主轴噪声降到73.5dB。
例2.主轴漏油
故障现象:
ZJK7532铣钻床加工过程中出现漏油
分析及处理过程:该铣钻床为手动换挡变速,通过主轴箱盖上方的注油孔加入冷却润滑油。在加工时只要速度达到400rpm时,油就会顺着主轴流下来。观察油箱油标,油标显示在油在上限位置。拆开主轴箱上盖,发现冷却油已注满了主轴箱(还未超过主轴轴承端),游标也被油浸没。可以肯定是油加的过多,在达到一定速度时油弥漫所致。放掉多余的油后主轴运转时漏油问题解决。外部观察油标正常,是因为加油过急导致游标的空气来不及排出,油将游标浸没,从而给加油者假象,导致加油过多,从而漏油。
例3. 主轴箱渗油
故障现象:CJK6032车床主轴箱部位有油渗出
分析及处理过程:将主轴外部防护罩拆下,发现油是从主轴编码器处渗出。该CJK6032车床的编码器安装在主轴箱内,属于第三轴,该编码器的油密封采用O型密封圈的密封方式。拆下编码器,将编码器轴卸下,发现该O型密封圈的橡胶已磨损,弹簧已露出来,属于安装O型密封圈不当所致。更换密封圈后问题解决。
例4. 加工件粗糙度不合格
故障现象:CK6136车床车削工件粗糙度不合格
分析及处理过程:在排除工艺方面的因素后(如刀具、转速、材质、进给量、吃刀量等),将主轴挡位挂到空挡,用手旋转主轴,感觉主轴较松。打开主轴防护罩,松开主轴止退螺钉,收紧主轴锁紧螺母用手旋转主轴,感觉主轴合适后,锁紧主轴止退螺钉,重新精车削,问题得到解决。
7.2数控机床进给系统的结构及维修
数控机床的进给传动系统的任务是实现执行机构(刀架、工作台等)的运动。大部分数控机床的进给系统是由伺服电动机经过联轴器与滚珠丝杠直接相连,然后由滚珠丝杠螺母副驱动工作台运动,其机械结构比较简单。
数控机床进给系统中的机械传动装置和器件具有高寿命、高刚度、无间隙、高灵敏度、和低摩擦阻力等特点。
7.2.1滚珠丝杠副
滚珠丝杠副是在丝杆和螺母之间以滚珠为滚动体的螺旋传动元件。它将电动机的旋转运动转化为直线运动。
1、 滚珠丝杠副的安装
数控机床的进给系统要获得较高的传动刚度,除了加强滚珠丝杠螺母本身的刚度之外,滚珠丝杠正确的安装及其支承的结构刚度也是不可忽视的因素。螺母座及支承座都应具有足够的刚度和精度。通常都适当加大和机床结合部件的接触面积,以提高螺母座的局部刚度和接触刚度,新设计的机床在工艺条件允许时常常把螺母座或支承座与机床本体做成整体来增大刚度。
滚珠丝杠副的安装方式最常用的通常有以下几种:
①双推——自由方式 如图7-2a所示,丝杆一端固定,另一端自由。固定端轴承同时承受轴向力和径向力。这种支承方式用于行程小的短丝杆。
重而出现的弯曲,同时丝杆热变形可以自由地向一端伸长。
③双推——双推方式 如图c所示,丝杆两端均固定。固定端轴承都可以同时承受轴向力,这种支承方式,可以对丝杆施加适当的预紧力,提高丝杆支承刚度,可以部分补偿丝杆的热变形。
2、滚珠丝杠副的防护及润滑
①滚珠丝杠副的防护 滚珠丝杠副和其他滚动摩擦的传动器件一样,应避免硬质灰尘或切屑污物进入,因此必须装有防护装置。如果滚珠丝杠副在机床上外露,则应采用封闭的防护罩,如采用螺旋弹簧钢带套管、伸缩套管以及折叠式套管等。安装时将防护罩的一端连接在滚珠螺母的侧面,另一端固定在滚珠丝杠的支承座上。如果滚珠丝杠副处于隐蔽的位置,则可采用密封圈防护,密封圈装在螺母的两端。接触式的弹性密封圈采用耐油橡胶或尼龙制成,其内孔做成与丝杆螺纹滚道相配的形状;接触式密封圈的防尘效果好,但由于存在接触压力,使摩擦力矩略有增加。非接触式密封圈又称迷宫式密封圈,它采用硬质塑料制成,其内孔与丝杆螺纹滚道的形状相反,并稍有间隙,这样可避免摩擦力矩,但是防尘效果差。工作中应避免碰击防护装置,防护装置一有损坏应及时更换。
②轴向间隙的调整 为了保证反向传动精度和轴向刚度,必须消除轴向间隙。双螺母滚珠丝杠副消除间隙的方法是,利用两个螺母的相对轴向位移,使两个滚珠螺母中的滚珠分别贴紧在螺旋滚道的两个相反的侧面上。此外还要消除丝杆安装部分和驱动部分的间隙。常
数控机床故障维修实例
篇二:数控机床皮带松动
数控机床故障维修实例
天津一汽夏利汽车股份有限公司内燃机制造分公司 杨琦
摘要:文中简述了关于数控机床故障的几个维修实例,如无法及时购到同型器件时的替代维修方法及与伺服、PLC相关的几个故障维修实例。
一、部件的替代维修
1.1丝杠损坏后的替代修复
采用FANUC 0G系统控制的进口曲轴连杆轴颈磨床,在加工过程中出现了411报警,发现丝杠运行中有异响。拆下丝杠后发现丝杠母中的滚珠已经损坏,需要更换丝杠。但因无法马上购到同样参数的丝杠,为保证生产,决定用不同参数的丝杠进行临时替代。替代方案是:用螺距为10mm的丝杠替代导程为6mm丝杠,且丝杠的旋向由原来的左旋改为了现在的右旋。为保证替代可以进行,需要对参数进行修正。但由于机床的原参数 P8184=0、P8185=0,所以无法通过改变柔性进给齿轮的方法简便地使替代成功,需根据DMR,CMR,GRD的关系,对参数进行修正。
对于原来导程为6mm的丝杠,根据参数P100=2,可知其CMR为1,根据参数P0004=01110101,可以知道机床原DMR为4,而且机床原来应用的编码器是3000pulse/rev。而对于10mm的丝杠,根据DMR为4,只能选择2500线的编码器,且需将P4改变为01111001。
同时根据:计数单元=最小移动单位/CMR;计数单元=一转检测的移动量/(编码器的检测脉冲*DMR)
可以计算出原机床的计数单元=6000/(3000*4)=1/2,即最小移动单位为0.5。在选择10mm的丝杠后,根据最小移动单位为0.5,计数单元=10000/(2500*4)=0.5/CMR,所以CMR=0.5则参数 p100=1。然后将参数p8122=-111,转变为 111后,完成了将旋向由左旋改为了右旋的控制,再将P8123=12000变为10000后完后了替代维修。
1.2用α系列放大器对C系列伺服放大器的替代
机床滑台的进给用FANUC power mate D控制,伺服放大器原为C系列A06B-6090-H006,在其损坏后,用α系列放大器A06B-6859-H104进行了替代。替代时,首先是接线的不同,在C系列放大器上要接入主电源200V、急停控制
100A、100B,地线G共6颗线;而对于α系列放大器,要接入主电源200V,没有接100A、100B,而是将CX4插头 的2-3进行短接来完成急停控制,然后将拨码开关SA1的1、2、3端设定在ON,拨码4设定在OFF后完成了替代维修。
伺服放大器部分的接线示意图
1.3完成回参考点的动作
对于有固定挡块回参考点的控制原理为,系统在接收到减速信号后,找到第一个一转零脉冲或第一个栅格点,即确认为参考点位置。
故障1:发生故障的机床采用的是巴鲁夫带接插头的接近开关来控制完成回参考点的动作,但由于接插线路出现断路,回参考点的动作无法完成,为完成机床调整的相关步骤,当时借用了临近的相同接近开关的接插线路,通过拔、插动作模拟完成了回参考点的过程。
故障2: 磨床修整器的伺服电机经皮带连接带动丝杠转动,在修整过程中发现位置偏差,分析应是参考点位置发生变化造成。查找后发现皮带松动,在通过改变中心距离的方法紧固皮带后,进行了返回参考点的动作,但修整位置仍然不对,在改变了坐标系的偏移量后,位置正确。故障应是由于电机位置改变造成丝杠的位置改变,从而返回参考点的第一个零脉冲的位置改变,改变的值应该是一个螺距的距离。
2.与驱动相关的故障维修
2.1 机床同时出现416、426报警
机床采用FANUC 0GE系统控制,最初的故障为机床CRT、伺服都不上电,经查为系统提供电源的电源单元损坏,在更换了新的电源后,CRT显示X、Z轴416、426号(位置环连接错误)报警。此报警一般与线路连接故障、伺服放大器故障、PCB板等的损坏有关。因为2个轴同时出现报警,根据经验,初步判定伺服放大
器及速度控制PCB板同时损坏的可能性不大,应从外部线路查找故障原因。通过分析对PCB的控制原理图,可以发现,伺服系统所需要的15V、24V、指示灯等的电压都是是由伺服变压器18V的电压提供的。伺服变压器所提供的18V电压,通过CN2接口提供给速度控制PCB板的工作所需。在查找外部线路后,发现是电源变压器的进路保险损坏后造成18V未给出,从而造成报警。
伺服控制原理图
2.2放大器过载报警
机床采用日本东荣伺服放大器控制,故障现象为运转准备后,能够实现伺服电机的锁住,但在handle进给移动过程中,机床出现较大震动后,瞬间出现伺服偏差过大报警及伺服放大器AL18(负载过载)报警,机床停止。首先检查了伺服电机、伺服放大器,但都没有问题,为此曾怀疑是NC系统或通讯线路有问题。但在MDI方式下监视到手动转动1圈丝杠的反馈脉冲数只有50000pulse,而实际应该为100000pulse(10mm),为此用示波器检查了编码器的反馈脉冲,在从NC板观测输入输出回路的波形时发现B 相脉冲不完全,出现了部分丢失,为此更换了编码器,故障解决。此故障可从三环控制原理进行解释,故障是由于位置反馈的脉冲丢失,致使NC系统需不断增加脉冲数,从而造成了电流值增加,从而出现伺服过载检测报警。此故障加深了对伺服控制原理的理解也拓宽了分析解决故障的思路。
2.3 机床950#(短路)的报警
机床采用FANUC 0T 控制,在机床上电后显示950#即保险断的报警,检查后是输出回路保险短路,所以应是外部线路的问题,同时由于是一合闸便有,所以应着重查找应用闭点的开关线路。首先查找的是机床X、Y轴的超程保护开关线路,最终查明故障是由于X 轴的超程保护开关的24V对地造成的。提出这个故障主要是说明对于故障查找应首先根据故障现象进行分析,有侧重点的查找,特别是对于短路故障的查找,如果没有目标的查找,将会造成时间的浪费。
2.4 机床9031(主轴受到束缚,无法按指令速度旋转)报警
机床为卧式加工中心,采用FANUC 18iM控制,主轴最高转速为8000转,采用高低速控制,在低于3000转/分时,是低速控制交流接触器吸合,高于3000转时高速交流接触器控制吸合。故障现象为机床在上电后执行空运转时出现了9031报警。
在MDI方式下,如果输入M19主轴定向,会出现9031报警,但如果输用M03S**,则只有转速在5000转时才会出现9031报警。9031报警是指电机无法按指令速度旋转,而是停止或以极低转速旋转,所以应该是定位有问题或者是主轴功率不够。由于机床已经正常运转过,所以不会是参数设定、电机相序的问题。有可能为电机的反馈电缆或动力线故障(主轴切换输出时电磁接触器是否打开)故障。最终查找为控制高速运转的交流接触器的上口进电的动力线松动造成。
2.5 SIEMENS伺服电源单元的报警
在西门子611A的伺服电源模块上有6个LED灯,分别代表不同的含义。
1:+/-15v电源供给错误
:5v电源供给错误
4 3:未准备好
:电源准备好(DC link charged)
5 6 5:供给错误
:直流过电压DC link over voltage
故障现象为,机床在上电后,在进行4个轴返回参考点的确认过程中,电源单元出现5号的红灯报警。为判断是电源单元本身的故障还是外部的故障,所以首先进行了单轴运动。其他3个轴在进行回参考点的运动时,电源不报警,只有第4轴回参考点时出现报警,所以排除了电源单元的故障。查找后发现第4轴在回参考点的过程中,无法准确定位造成了电源报警。在将回参考点的速度降低后,故障消除。
3、与PLC相关的故障
3.1与输入、输出相关的故障
机床由西门子S5的PLC 控制,且输入、输出部分采用ET200 来控制。故障的表现为,在机床运转中输出点Q72.0会出现突然掉电现象,同时PLC 的BF(bus fault)灯亮,ET200处出现IM fault 灯亮。
首先查找外部线路问题,由于ET200处出现IM fault 灯亮,所以首先查找了ET200处的I/O 模块。在更换I/O模块时发现,连接线缆有部分破损现象,更换后IM fault 灯熄灭,但输出点Q72.0仍然出现不固定的断电的故障。在进行PLC联机测试时发现M11.5断续出现断电现象的原因是K2100有断电现象,而输入点I33.0对应K2100,由于已经更换了输入输出模块,所以只能通过变更输入点来进行解决,在将输入点改变后,故障消除。改变输入点时,应注意此输入点在其他功能模块中的引用,应全部变更。
3.2 S5程序的重新启动
在进行修改S5 的PLC程序后,一般只需对原程序进行覆盖,便可正常启动PLC;但若是因为电池没电造成的PLC停止,在进行PLC的程序传输后,会出现无法启动PLC,这时需要选择PLC菜单,点击其下的PLC Start才能使PLC重新运转。
3.3 SIEMENS 840C 系统上电后出现 43 PLC–CPU not ready for operation报警
机床为SIEMENS 840C系统控制,系统上电后,进行自检时出现43 PLC–CPU not ready for operation报警,查找PLC其显示状态正常,进行general reset中的PLC RESET后故障依旧。最终查找故障原因是机床应用的手持单元中,有一个接口虚接造成,重新拔插后故障消除。
数控故障维修
篇三:数控机床皮带松动
数控机床故障诊断与维修数控机床皮带松动。
模块一:
1、数控机床组成部分及各部分的作用:
CNC、计算机数控装置、伺服驱动装置、机床本身、数控系统、辅助装置。
2、浴盆曲线的三个阶段的名称,故障率的变化规律:
三个阶段:早期故障期、偶发故障期、耗损故障期;故障率:高→低→平稳→高 浴盆曲线:
3、机床故障的外因:供电电压过低、过高或波动过大;电源相序不正确或电压不平衡;环境温度过高;有害气体、潮气、粉尘侵入引起的短路;外来震动和干扰等。
4、数控机床故障排除思路:①掌握信息,寻找特征②据理析象,判断类型③罗列成因,确定步骤④合理测试,故障定位⑤排除故障,恢复设备
5、故障排除应遵循的原则:①先外部后内部②先机械后电气③先静后动④先公用后专用⑤先简单后复杂⑥先一般后特殊⑦先查输入后查负载⑧先软件后硬件
6、直观法和交换法
直观法:①问(操作者)②看(元器件及线路)③听(机床响动)④触(是否有震动、发热)⑤嗅(是否有糊味)
交换法:在数控系统中当有型号完全相同的电路板、模块、集成电路和其他零部件时,才可以使用交换法
7、常用的测量量具的应用:①条式水平仪②杠杆百分表③游标卡尺④大理石方尺
8、点检作用:减少故障重复出现率,能早期发现机床的隐患和劣化程度,以便及时采取有效的措施;还可以使操作人员接班内容具体化、规范化,易于执行。
9、点检内容:①定点②定标③定期④定项⑤定人⑥定法⑦检查⑧记录⑨处理⑩分析
模块二:
1、导轨分类(根据其接触形式):滑动导轨、滚动导轨
2、导轨作用:支撑、引导
3、导轨间隙位置及调节方式:?侧面(利用镶条调节)?上下支撑面(用压板调节)
4、直线导轨副的安装于调试过程:
①在安装前先用水平仪检测导轨底座的水平②将一侧导轨安装并预紧,用深度尺粗测导轨与底座侧面的平行度③在用杠杆百分表精测导轨与底座侧面的平行度,并用橡皮锤调整导轨的位置④固定导轨,再用杠杆百分表检测导轨与底座侧面的平行度⑤将另外一侧的导轨预紧,用游标卡尺粗测两导轨之间的平行度,再用杠杆百分表精测两导轨之间的平行度。再用杠杆百分表确定两导轨之间的等高度⑥固定导轨,再用杠杆百分表检测两导轨之间的平行度和等高度
5、滚珠丝杠螺母副的作用:是数控机床理想的运动转换装置,即可将直线运动变成旋转运动,也可将旋转运动变成直线运动。
滚珠丝杠螺母副的组成:轴承支座、角接触球轴承、轴承盖、螺母座、螺母、丝杠、深沟球轴承、电机支座、轴承盖
6、螺距误差、反向间隙误差可采用双向螺距误差补偿法。
7、滚珠丝杠螺母副间隙调整的方法:①双螺母消隙(垫片式、螺纹调整式、齿差调隙式)②单螺母消隙变位导程自预紧式③弹簧式自动调整预紧式
8、滚珠丝杠螺母副的预紧是为了提高刚度和反向传动精度。
9、主轴系统的作用:产生主切削力
10、主轴在强力切削时停转,产生的原因:①皮带松动②皮带表面有油③皮带磨损疲劳失效④摩擦离合器过松或磨损
11、机械十字滑台的作用是进给运动的执行部件。
12、工作台在X方向位移接近终点过程中产生明显的机械振动故障,故障发生时,系统不报警,试分析其原因:
故障可能原因:①直线导轨副安装时两导轨之间不平行或不等高。
②滚珠丝杠螺母副在安装时螺母损坏 ③丝杠破损或丝杠上的螺纹损坏 模块四:
1、FANUC系统端口定义及接线
?工作电源(CP1端口 24V/DC)
?主运动系统(模拟/串行)数控机床皮带松动。
①模拟主轴系统:
②串行主轴系统:
(3)进给系统:FSSB(FANUC系统数据控制总线)光缆,串行伺服总线。
(4)I/O LINK(JD51A端口)→I/O LINK(JD1B端口)
(5)其他(风扇、电池、软键、MDI等)(伺服检测口CA69端口,不需接线)
(存储卡插槽 CF卡)(RS232端口 与电脑通信端口)
2、数控系统启动不了,分析发生该故障的可能原因:(FANUC系统上电原理图不用画)
可能原因:
3、FANUC数控系统参数备份的方法:①引导系统参数备份②系统数据分别备份
4、参数设定的步骤:①在“MDI”或急停模式下,解除保护方式(即按“SYSTEM”键一下或多下,直到出现“设定”画面,将“写参数”设定为“1”)数控机床皮带松动。
②按MDI面板上的功能键“SYSTEM”几次或一次后,再按软键“参数”选择参数画面 ③用键盘输入##,然后按软键“检索”④将##号参数数值设定为X
⑤开启保护方式,即将“设定”画面里的“写参数”设定为0 ⑥重启FANUC系统
5、(已知1023=01011100)求1023#6=? 1023#6=1
6、进给伺服系统的组成:伺服驱动器、伺服电机
7、进给私服系统的作用:接受CNC发出的进给运动指令,经过转换和放大后驱动伺服电机
8、FANUC β iSVM20 伺服驱动器端口定义及接线:
(1)动力线端口:入口(L1/L2/L3 三相380VAC) 出口(U、V、W 三相380VAC) 输入(CX19B 24VDC) 输出(CX19A 24VDC)
(2)与CNC的通信端口接线:
(3)电机反馈端口:JF1
(4)CX29:驱动使能端口
9、伺服驱动器强电指示灯不亮,分析发生该故障的可能原因:(电气原理图不用画)
可能原因:[考试时主要内容为:故障分析及其故障原因,其他皆可省去]?各处元器件接线接触不良?开关SB1、KM0、QS1、KM1、KA1未闭合?24V/DC电源未接通?驱动使能端CX29未闭合,?各熔断器不正常
10、全清系统参数操作:操作之前一定要做好参数备份,同时按“RESET”+“DELETE”全清系统参数,重新启动数控系统后出现系统报警画面。 11、参数设定支援画面:
①全清系统参数,修改语言,设置中文操作画面.
②连续按{SYSTEM}键3次进入轴设定支援画面.
③将光标移到伺服设定上,按{操作}键进入{选择}界面,按向右扩展键进入菜单与{切换}画面,进入轴设定初始画面.
④按下软键{初始化},进入轴设定初始化执行画面,显示警告信息”是否设定初始值?”
⑤按下软键{执行},系统自动的将项目中包含的参数设定为标准值(FANUC建议使用的值)。没有提供标准值得参数,不会变更。
12、模拟主轴与串行主轴的区别:?模拟主轴:通过CNC内部附加的D/A转换器,自行将S指令转换为-10V到+10V的模拟电压(JA40)?串行主轴:通过CNC输出的控制指令也可以通过网络进行传输,在CNC与主轴驱动器之间建立通信,这一通信一般使用CNC串行接口,
13、变频模拟主轴系统由变频器和步进电机组成。
14、三菱变频器端口定义及接线(模拟电压端口,STF、STR)
?控制电路端子:①模拟电压值(0~10V 2、5端口)②正反转端子(STF正转 STR反转)?主电路端子:三相380VAC(L1/l2/l3输入 、 U/V/W输出 、 进入步进电机)
15、变频模拟主轴系统,主轴不转,分析发生故障可能的原因(电气控制原理图)
答:故障原因可分为主电路和控制电路。
①用万用表检测L1、L2、L3主电路是否连接正常,用万用表查个元器件连接是否正常,是否有松动等问题;检测电元器件,如熔断器,中间继电器是否损坏。
②Y8.0/Y8.1是否有输出; I/O诊断看Y8.0是否为1或Y8.1是否为1; 用万用表检测KA2/KA3触电元件是否有损坏。
③查看JA40端口及变频器2、5端口是否有电压输入,输出,用万用表查看是否有电压值。
④主轴旋转条件的问题是否得到满足。
16、变频器的某些参数(P1、P7、P73、P79)
17、I/O LINK端口定义及接线:
?工作电源(CP1 24V/DC)?操作面板 CB107 CB105?CB104→A18(Y8.5)
?JD1B→JD15A 【I/O LINK(JD1B)→中间继电器→接近开关、霍尔元件】
18、数控系统的信号定义:
X:来自机床侧的输入信号(如接近、极限开关、操作按钮等输入信号元件)地址从X0开始 Y:由PMC输出的机床侧的信号,输出信号在机床侧的电磁阀、接触器等)地址从Y0开始 F:由控制伺服电机与主轴电机的系统部分侧输出到PMC信号,地址从F0开始
G:由PMC侧输出到系统部分的信号,对系统部分进行控制和信息反馈,地址从G0开始
19、I/O单元的物理地址定义方式:组、基板、槽